铜箔胶带使用的材料
铜箔带是一种多用途材料,由于其独特的性能和在需要导电性,屏蔽性和粘附性的应用中的有效性,广泛应用于各个行业。铜箔胶带的构造涉及几种关键材料,每种材料都有助于其整体功能和性能。
下面我们将深入了解铜箔胶带中使用的材料,包括铜箔本身,粘合剂背衬,可选涂层及其各自的性能。
Table of Contents
1.铜箔
材料组成:
铜:铜箔胶带的主要成分是铜,一种以其优异的导电性和导热性而闻名的金属。选择铜是因为其优越的导电和导热能力,使其成为需要有效电连接或散热的各种应用的理想选择。
厚度:胶带中使用的铜箔通常非常薄,厚度范围从1密耳(0.001英寸)到几密耳。根据应用要求选择特定厚度,较薄的箔更灵活,较厚的箔提供更高的耐用性和屏蔽效果。
光洁度:铜箔可以有不同的光洁度,包括光泽、哑光或拉丝。表面处理会影响胶带的外观和性能。例如,有光泽的表面可能为某些屏蔽应用提供更好的反射率,而哑光表面可能提供更柔和的美学。
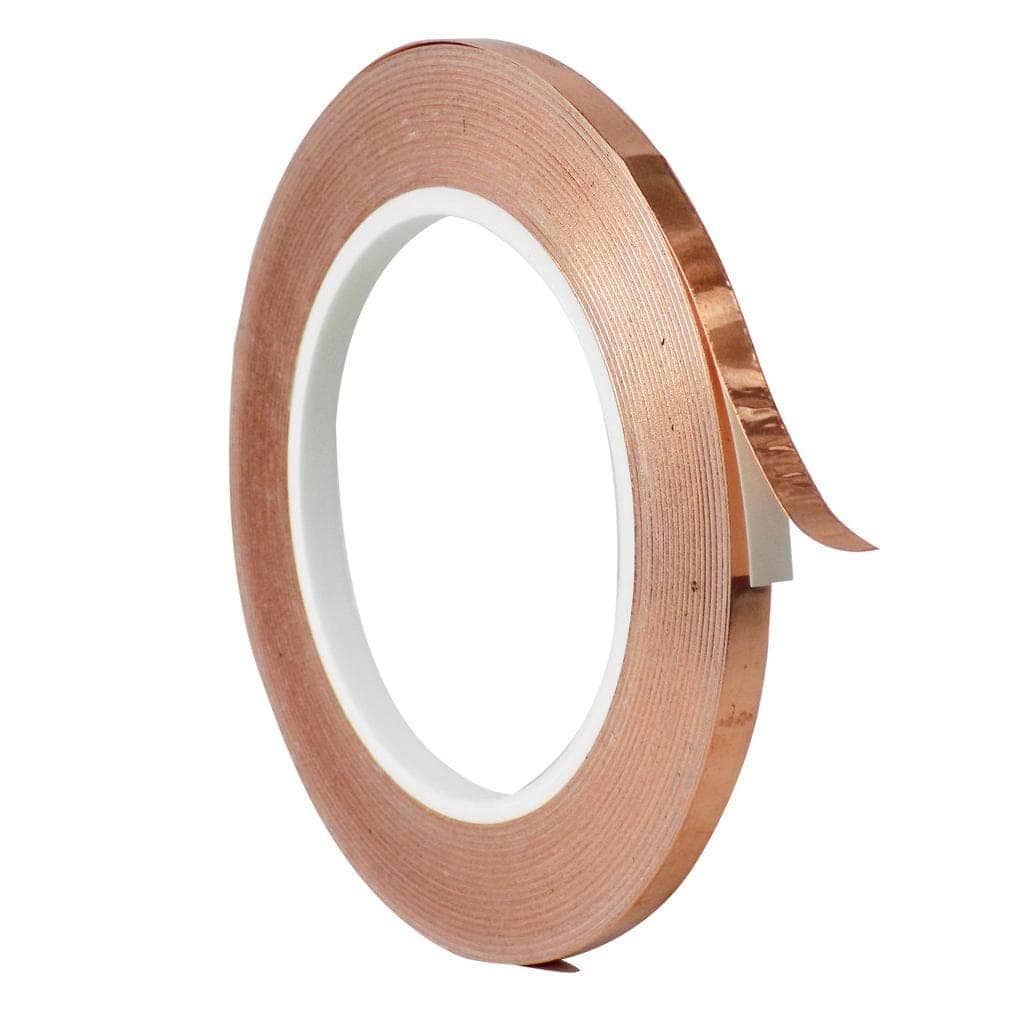
特性和优点:
导电性:铜是一种优良的导电体,对于接地、屏蔽和电路修复等应用至关重要。铜的高导电性确保了电信号和电流的有效传输,最大限度地减少了损耗和干扰。
灵活性:铜箔的薄性质使其具有高度的灵活性,能够适应各种表面,包括弯曲或不规则的形状。这种灵活性允许铜箔胶带在狭窄的空间和复杂的设计中使用,例如在电子和工艺项目中。
导热性:铜除了具有导电性外,还具有优良的导热性。这种特性使铜箔胶带适用于涉及散热的应用,例如热管理系统或散热器。
耐腐蚀性:随着时间的推移,铜会自然氧化,这会导致生锈和降解。为了解决这个问题,铜箔通常经过处理或涂覆,以提高其抗腐蚀性,并随着时间的推移保持其性能和外观。
2. 粘合底布
材料组成:
粘合剂类型:铜箔胶带上使用的粘合剂根据应用和所需的性能特性而有所不同。常见的粘合剂类型包括丙烯酸、橡胶和硅树脂。
丙烯酸胶粘剂:以其强附着力、耐久性、耐老化和抗紫外线而闻名。丙烯酸胶粘剂提供永久粘合,适用于各种表面和应用。
橡胶基粘合剂:对各种表面具有良好的初始粘性和附着力。橡胶基粘合剂通常用于需要快速和牢固粘合的应用,尽管它们可能不具有与丙烯酸或硅树脂粘合剂相同的耐温水平。
硅酮粘合剂:提供耐高温性能,通常用于涉及极端高温或暴露于化学品的应用。硅酮胶在高温环境下也能保持良好的粘接性能,受温度波动的影响较小。
背衬材料:一些铜箔胶带有背衬材料,如纸或塑料,在胶带使用之前可以保护粘合剂。在使用前去除底衬材料,确保粘合剂在使用前保持清洁和有效。
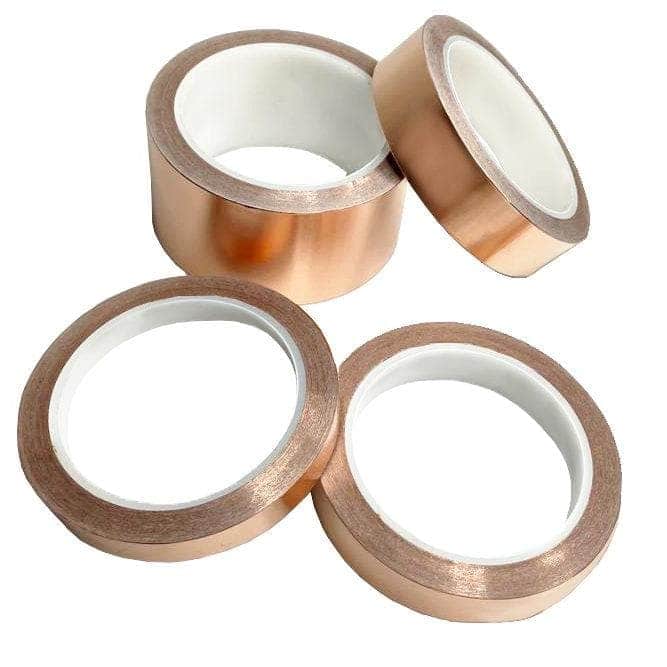
特性和优点:
附着力:胶背设计为各种表面提供强大,可靠的附着力,包括金属,塑料,陶瓷和玻璃。这样可以确保胶带牢固地固定在适当的位置并执行其预期的功能。
耐温性:根据粘合剂类型的不同,铜箔胶带可以承受一定范围的温度。例如,丙烯酸胶粘剂通常在中等温度下表现良好,而硅酮胶粘剂更适合高温环境。
易于应用:大多数粘合剂的压力敏感性质允许易于应用和重新定位。此功能对于在粘合剂永久粘合之前需要精确放置或调整的任务特别有用。
3.防锈涂层(可选)
材料组成:
涂层材料:部分铜箔带表面涂有防锈层,防止氧化和失去光泽。常见的涂层包括有机化合物、聚合物或其他抑制氧化铜形成的保护层。
目的:防变色涂层的主要目的是随着时间的推移保持铜箔的外观和性能。这在视觉美学和长期可靠性至关重要的应用中尤为重要。
特性和优点:
增强耐用性:防变色涂层有助于保护铜箔免受环境因素的影响,如湿度、空气暴露和化学相互作用。这种保护延长了磁带的使用寿命,并确保了一致的性能。
耐腐蚀:通过防止氧化,涂层保持铜的导电性能,防止胶带因腐蚀而失去其有效性。
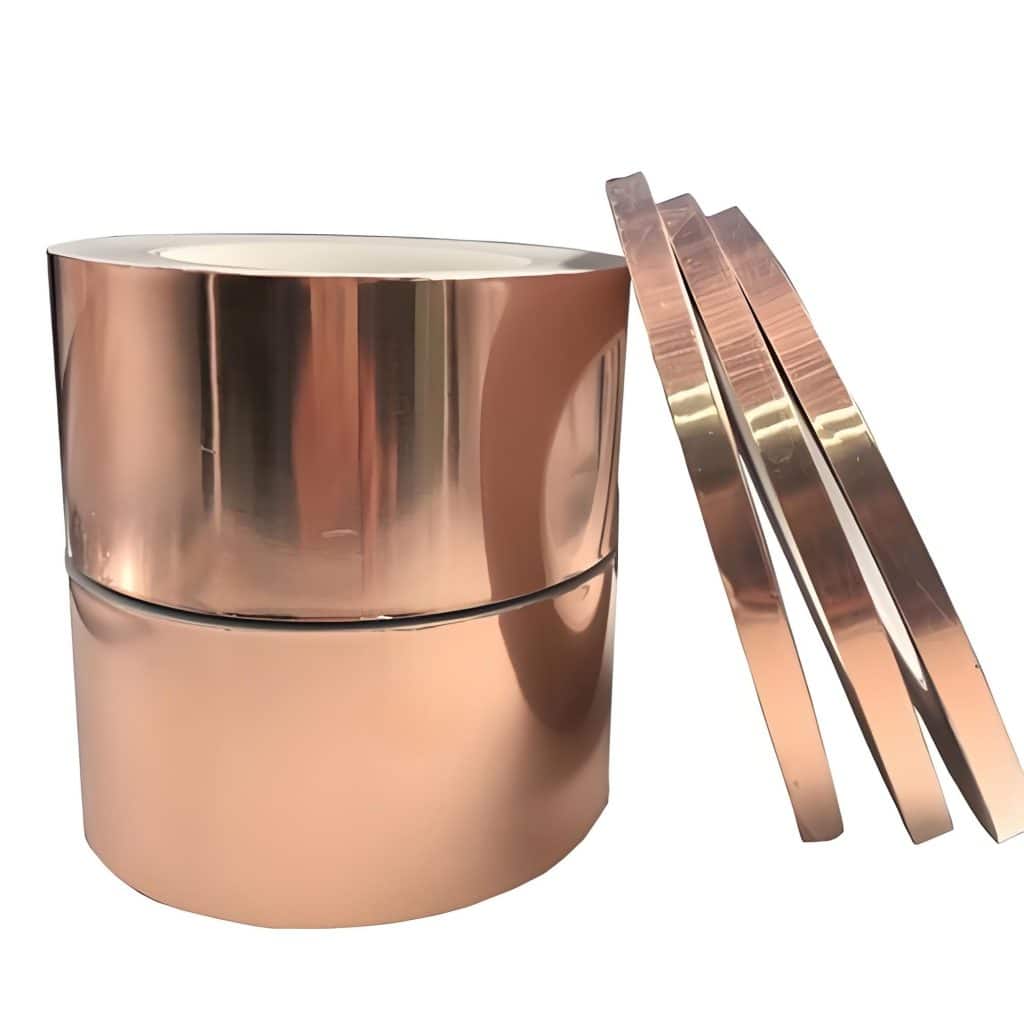
4.额外的注意事项
环境影响:
可回收性:铜是一种可回收的材料,许多铜箔胶带使用后可以回收,减少了对环境的影响。胶带的可回收性取决于粘合剂和涂层材料,这可能会影响整个回收过程。
合规和标准:
行业标准:铜箔胶带必须符合各种行业标准和法规,如电子产品的RoHS (Restriction of Hazardous Substances)和化学品安全的REACH (Registration, Evaluation, Authorization, and Restriction of Chemicals)。合规性确保磁带满足其预期应用的安全和性能要求。
5.总结
铜箔提供优良的导电性和导热性,而粘合剂的背衬确保强附着力和易于应用。可选涂层增强胶带的耐久性和耐腐蚀性。这些材料一起工作,使铜箔胶带成为广泛应用的通用和有效的解决方案,从电子和工业用途到工艺和家装项目。 了解材料及其特性有助于用户根据其特定需求选择合适的铜箔胶带,确保最佳性能和可靠性。 翰达岛屏蔽 提供优质的定制铜箔胶带,如果您有需要,请立即与我们联系。
您可能也会喜欢
-
EMI/EMC/RFI 屏蔽解决方案
EMI 铍铜和不锈钢屏蔽簧片/弹片
介绍 直角屏蔽指带,也称为角度指带,是专门设计用于管理电子系统中的电磁干扰(EMI)和射频干扰(RFI)的组件。这些指带在电子元件以90度角相交的配置中特别有用。它们的主要作用是确保有效的屏蔽,保持电磁兼容性(EMC)和保护敏感的电子设备免受干扰。 设计与功能规格及材料安装注意事项生产过程好处结论 设计与功能 目的及重要性 直角屏蔽指带的主要目的是在垂直元件布置的电子装置中提供可靠的EMI/RFI......
-
导电铝/铜箔和导电布
铜箔胶带
铜箔带, 是一种广泛应用于电子设备中以防止电磁干扰(EMI)和射频干扰(RFI)的 屏蔽材料 ,包括一层铜箔层压在柔性基板材料(通常是聚乙烯或聚酯)上,并在背面具有导电粘合剂。这种胶带的设计目的是建立一个防止不良电磁场的屏障,有效地屏蔽内部组件免受外部干扰,反之亦然。 以下是铜箔胶带在不同行业和部门的各种应用的全面概述 电子及电气工程手工艺和艺术工业应用汽车工业航空航天医药设备DIY和家居装修科学......
-
新闻中心
射频/EMI屏蔽螺旋垫圈 是专门设计用于保护电子设备免受电磁干扰(EMI)和射频干扰(RFI)的组件。了解这些垫圈的工作原理包括掌握电磁干扰屏蔽原理和螺旋垫圈的独特结构。 了解电磁干扰(EMI)和射频干扰(RFI)电磁干扰(FWI)射频干扰(RFI)EMI/RFI屏蔽的重要性射频/EMI屏蔽螺旋垫圈的作用射频/EMI屏蔽螺旋垫片的设计与构造电磁干扰屏蔽螺旋垫圈如何阻挡电磁干扰RF/EMI屏蔽螺旋垫......
-
新闻中心
介绍RF/EMI屏蔽螺旋垫圈的应用:射频/EMI屏蔽螺旋垫圈的好处:瀚达屏蔽的RF/EMI屏蔽螺旋垫圈类型:总结 介绍 RF/EMI屏蔽螺旋垫圈是电子和电气设备领域的关键部件。它们旨在保护敏感设备免受电磁干扰(EMI)和射频干扰(RFI)。这些垫圈通过保持信号完整性和屏蔽外部干扰来确保电子系统的最佳性能和寿命。在这个全面的探索中,我们将深入研究射频/EMI屏蔽螺旋垫圈的各种应用,它们的好处,以及它......
-
EMI 铍铜和不锈钢屏蔽簧片/弹片
夹式安装屏蔽簧片
产品描述 瀚达屏蔽科技公司是业内领先的屏蔽材料供应商之一,生产几乎覆盖所有相关应用领域的电磁屏蔽和导电材料。指形垫圈是一种常见的金属屏蔽垫,在结构上可分为粘贴式安装屏蔽门簧片和夹式安装屏蔽簧片。粘贴式安装屏蔽门簧片通常更适合安装在狭窄的空间内。然而,在某些特殊的应用环境中,如高温环境,由于压敏胶的温度适应性,粘贴式安装屏蔽门簧片将不再适用。因此,瀚达屏蔽开发了一系列夹式安装屏蔽簧片来满足这些特殊的......